Image
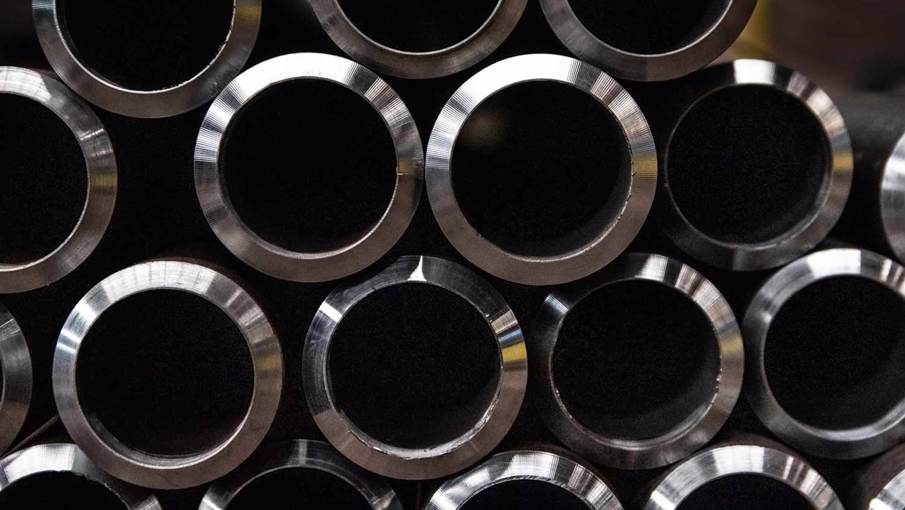
Renewable energy has a significant role to play in cutting carbon emissions in metal industries.
Using fossil-free energy in the iron and steel industries would have a powerful impact on carbon emissions. Carbon capture technology is another option.
Figures from 2018 record global steel production at 1.8 gigatonnes (Gt), with China accounting for more than half of this amount. Every tonne of steel produced generates approximately 1.8 tonnes of CO2 emissions – generating a global total of 3.1 Gt, including both direct and indirect emissions. This represents 8% of total energy- and process-related CO2 emissions.
More than two thirds of steel is produced via Blast Furnace-Basic Oxygen Furnace (BF-BOF), which uses metallurgical coal as a chemical-reduction agent. Most of the remainder is produced via electric arc furnace (EAF) from direct reduced iron (DRI) or steel scrap.
Direct and indirect emissions from the aluminum industry account for 0.4 Gt of CO2 – around 1% of total energy- and process-related CO2 emissions. Some 90% of aluminum-industry emissions are indirect, coming from electricity used in production. The remaining 10% of emissions comes from the carbon anodes used in the process.
There are a number of ways we can support the metal industries to reduce their carbon footprint.
Tabs
The iron and steel industry has two main options for decarbonizing to net zero:
- Switching to direct reduced iron (DRI)/electric arc furnace (EAF). This involves replacing the blast furnace process – which uses both carbon and coke to remove the oxygen from iron ore – with a direct-reduction process that uses fossil-free energy to produce hydrogen from water. The only by-product is water vapor. At least six plants, mostly in Europe, are piloting this process.
- Applying carbon capture, utilization and storage (CCUS) to existing processes. The second option means continuing to use processes based on fossil fuels. Carbon-capture equipment is installed to capture the majority of CO2 emissions. The carbon is then transported to permanent storage, or can be used in synthetic fuel production, for example.
The only option for decarbonizing aluminum to net zero is to source all electricity and heat from renewables and replace coal-based anodes with sustainable alternatives.
We can support the iron and steel industry’s decarbonization efforts by:
- Building captive power plants based on the non-recyclable fractions of biomass residues and waste.
- Providing carbon-capture solutions through calcium looping.
And we can support the aluminum industry’s green transition by providing industrial thermal power plants that run on biomass. We’re also exploring ways of replacing coal-based anodes with biochar.
When using dedicated renewables for electricity generation, Liquid Air Energy Storage (LAES) technology can solve intermittency issues to ensure reliable power generation.
We can support metals producers’ efforts to minimize their carbon emissions. It is a challenge they can overcome and in doing so have a serious impact on the drive to net zero.